Sunday8.6 hours this weekend, no rivets.
Strip plastic from outside of left rudder skin
Cut left stiffeners to length
Trimmed left stiffeners, deburred edges
Cleco and match drilled left stiffeners/skin
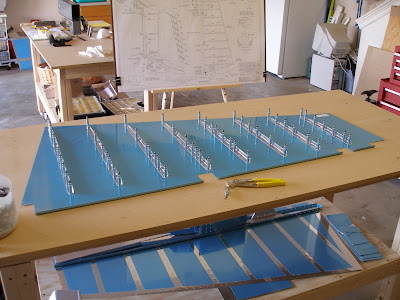
Cleco and match drilled right stiffeners/skin
While I had the bandsaw out, finished the rough fabrication work for several misc. pieces: Cut out R917 shim, cut out R918 bottom attach strips, and trimmed R710 horn brace
Saturday
Got the taxes to a reasonble stopping point, so treated myself to building as a reward. Didn't do any thing on the plane Friday night, first day with no time in 3 weeks!
Pulled Rudder parts
Stripped outside of right skin
Cut stiffeners from stock.
FAA mandated inspection...
Trimmed and sanded right stiffeners
Cut right stiffeners to length
Deburred edges of right stiffeners
After finishing for the day, Lynne and I went out for the evening, our first time out being adults in a long time. Lynne just started working on a Masters in Education, so she has no real life either. After dinner with a few other people, we met with our group of friends on the steps of the Texas Capital, which had closed for the night. No problem, one of the friends works security for the building. We were treated to the most amazing evening of sights that most people will never see.
There's this cool old vault in the basement, with a heavy door with complicated locking mechanisms, the whole nine yards. It has this hallway that goes completely around it. There are mirrors arranged in the corners so that you can see all the way around. How cool is that! They keep door locks and fanbelts (for DPS cars) in the vault now. What a waste of a state treasure.
Next we went up. Now the normal Texas Capital building tour goes up four flights to a balcony overlooking the rotunda. It's a dizzying perspective, looking down on the floor. The four levels are adorned with portraits of the Texas governers, the first being up at the top (still lots of room for more). But we weren't done.
Past a security rope and up a normal flight of stairs we went. Then it got interesting. We went outside on the roof for short walk, and then into the dome superstucture, then up a series of spiral staircases, though the interior and in the superstructure, ALL THE WAY TO THE TOP.
If my arms were three feet longer, I could have touched the star on the ceiling of the rotunda.
You can see one of the spiral staircases, at about the 5 o'clock position. We climbed that!
There are FAA lights in a bell housing just underneath the lady, above the star in the ceiling. We were in that section. But the lights were installed in the days before the laywers ruined everything, and had bare wires exposed. I'm too tall and didn't want our host to lose his job over an electrocution so I didn't stay up there too long. There's a very small balcony at the very top, at the base of the bell housing. We were up there. And we also walked around all of the obvious balconies in this picture.
A truly magnificent building.