This entry is for yesterday, Tuesday, December 30.
1.9 hrs, 44 rivets.
Riveted the rear spar to the wing frame. Some of the longer rivets on the inboard end are called out a bit too short. For instance the AD4704-6 rivets that attach ribs 3, 4, and 5 to the spar and doubler, really should be 6.5 in length. The 6's as called out on the plans just barely work, but 7's are too long. A better idea would be to cut 7's down to 6.5 And there are 7s and 8s that have the same issue. Time to get a rivet cutter.
Actually flew today! Got a landing in at Lakeway and then flew to Brenham for lunch. Met Mike Torbett. We didn't fly together because I was in a 152 and he was in this:
Mike Torbett and his Panzl
Brenham was a beehive. I still find a crowded traffic pattern to be a challenge. As we were walking into the diner, everyone was oohing and aahing over the Panzl. On departure, I left first, with him next. I could hear everyone going (appreciatively) nuts on the radio as he did a high performance climb (after it was requested by the audience). After departing, Mike caught up and flew with me for a little, close to his stall speed.
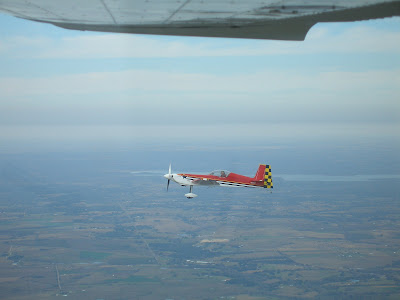
Hamburger at the Brenham Airport Diner: $200. First formation flying: Priceless!